A heated seat belt provides occupants with warmth in cold temperatures and may help e-vehicles get ahead. ZF’s latest innovation has an integrated technology that weaves the heating conductors into the seat belt structure.
Drivers of electric cars are familiar with the effect: as soon as the first sub-zero temperatures arrive, the batteries have to be recharged at shorter intervals. This is because cold temperatures can reduce the range of pure electric cars by up to 30 percent, in part because the battery works optimally between 20 and 40 degrees Celsius. In addition, occupant comfort eats away at the kilowatt hours because the heating system cannot draw on the waste heat of an internal combustion engine. Instead, the heat for the entire interior has to be generated from battery power.
The Electric Blanket Principle
ZF realized it would be much more efficient to warm occupants directly by means of electric heating elements – similar to an electric blanket. This is the principle used for heated seats and steering wheels. Now, for the first time, an innovation from ZF makes “all-around warming” of passengers possible. A heated seat belt warms the upper body and pelvic area evenly from the front. In combination with heated seats, the heated seat belt has the potential to provide occupant comfort quickly. In electric vehicles, the climate control system is powered by battery current, as there is no usable waste heat as with the combustion engine. Reducing the amount of battery current used to heat the interior of the vehicle, may enable a range gain of up to 15 percent.
Webbing With Special Weaving
The technical basis is more complex than it might seem at first glance. Only those who look very closely can see the difference from conventional belt webbing. Small wires, known as heating conductors, are woven directly into the belt structure like threads. The contact elements for the electrical heating circuits are positioned in such a way that they do not interfere with either the operation of the belt or the retractor.
“For the occupants, there is no difference in terms of operation when compared to a conventional belt,” explains Martina Rausch, who is responsible for new seat belt developments at ZF. “And, of course, the heated seat belt is in no way inferior to its conventional counterparts in terms of crash behavior,” Rausch emphasizes.
Car manufacturers can also be pleased. Installation differs only in nuances from that of conventional seat belts. Therefore, the heated seat belt can be used in series production. The advantage lies in the woven-in heating conductors. The thickness of the belt is unchanged - in contrast to other methods, such as a belt tube with a heating element.
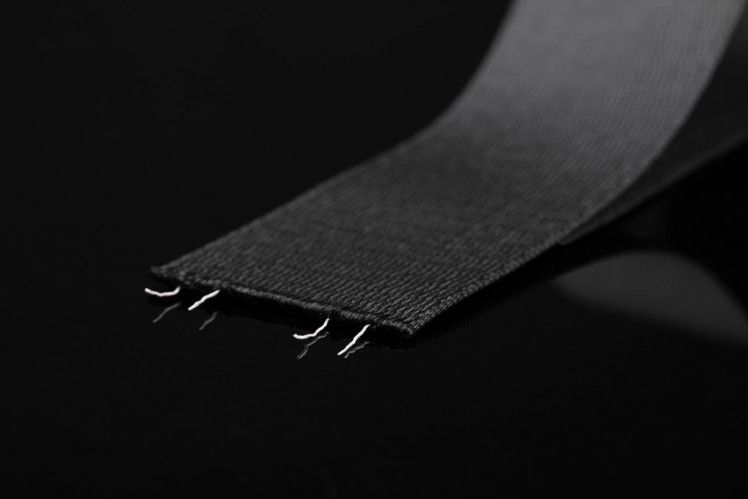
Warming Safety
The heated belt warms up immediately after the vehicle starts moving. The more directly the vehicle occupants allow this heat to reach their bodies, the better - and not only for the feeling of comfort, but also with no compromise in safety. “When the passengers take off their thick winter jackets, the seat belt lies closer and directly against the body and the restraint remains at optimal function in the event of a crash,” explains Rausch.
ZF’s innovation is in demand from automakers. No wonder - after all, it increases comfort, provides the same performance, and may increase range at the same time. And it shows: ZF is bolstering the spread of electromobility not only with technology for the driveline, but also from the interior - very close to the occupants.
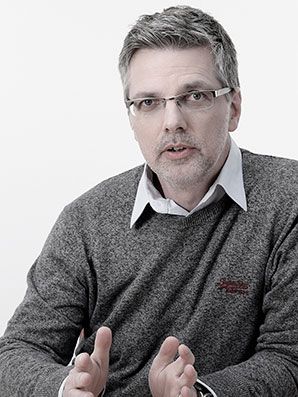
Andreas Neemann wrote his first ZF text in 2001 about 6HP transmissions. Since then, the automotive writer has filled many publications for internal and external readers, showcasing his passion for the Group's more complex subjects.
Next Stories
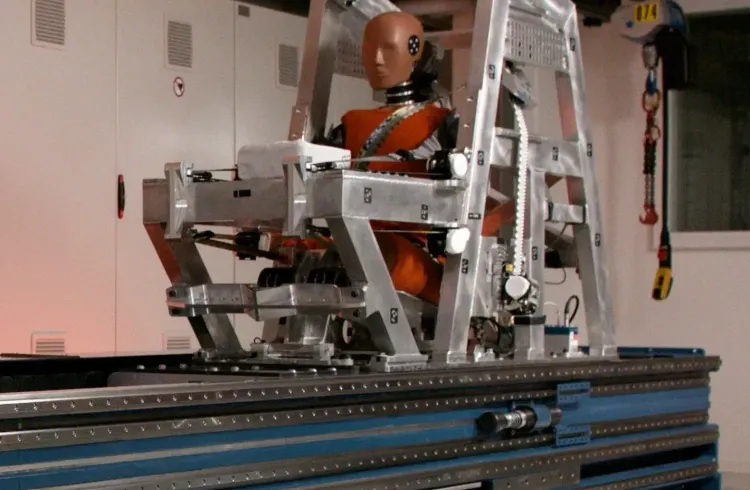
HyDRA®: Full electric crash-sled shortens development time
Precise sensors and digital interfaces allow HyDRA® to accelerate the development of seatbelt systems with highly dynamic testing. Reaching in near future a new level of adaptability - setting actively the safety system to match real-life conditions.
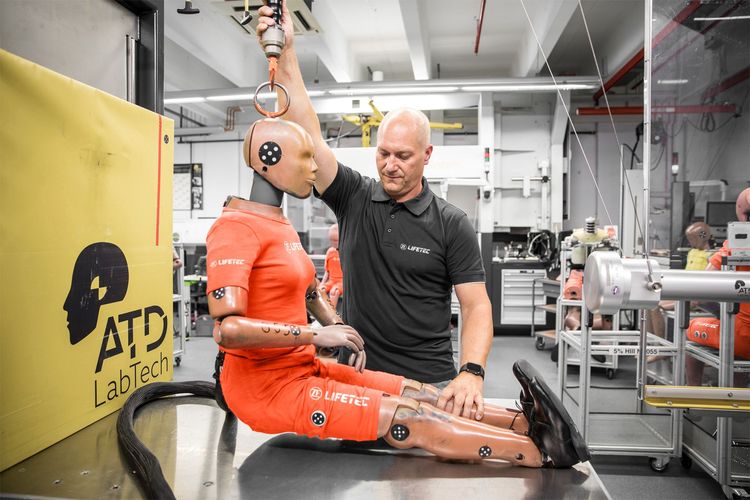
Behind the Scenes: Look into the Dummy Laboratory
When it comes to global occupant safety systems such as airbags and seatbelts, ZF is the leader, as is widely known.