Precise sensors and digital interfaces allow HyDRA® to accelerate the development of seatbelt systems with highly dynamic testing. Reaching in near future a new level of adaptability - setting actively the safety system to match real-life conditions.
The well-known Crash-Test-Dummy was introduced in 1976 as "50th percentile male". Subsequently a whole family of crash test dummies was developed (a “5th percentile woman” and three children) – yet expectations from society and new mobility requirements evolve rapidly. Men and women, who do not match in size, figure and mass to one of the “standard” dummies, require equity in safety as well as elderly people known to have more fragile bones. Also, highly automated driving will soon change the interior of vehicles, providing seating positions significantly different from existing configurations– while requiring the same high safety standards to be met. Finally, consumer protection organizations like NCAP are asking for expanded crash safety requirements despite the already high level of passive safety established by now.
Paradigm Shift: Passive Safety Systems, tailored to the occupant.
"The general trend in passive safety moves towards adaptive restraint systems able to respond more specifically to the actual accident scenario and the actual need for restraint forces", explains Dr. Kai-Ulrich Machens, Manager of Seat Belt Systems Engineering: Function Test Methodology, Materials & Acoustics at ZF LIFETEC in Alfdorf. Thanks to novel sensor systems in cars, the restraint systems control software could have access to significantly more information in the future: i.e. what kind of crash is occurring? What is the weight of the person in the driver seat? What is the weight of the occupant in the passenger seat? What is the occupant size? Is the occupant sitting straight, slouched, or leaning forward? This information is of value to set adaptive functions on the seatbelt system, for instance the restraint forces needed for optimal protection of a petite person in a frontal crash. Adaptive means everyone receives the passive safety that fits them and their situation specifically.
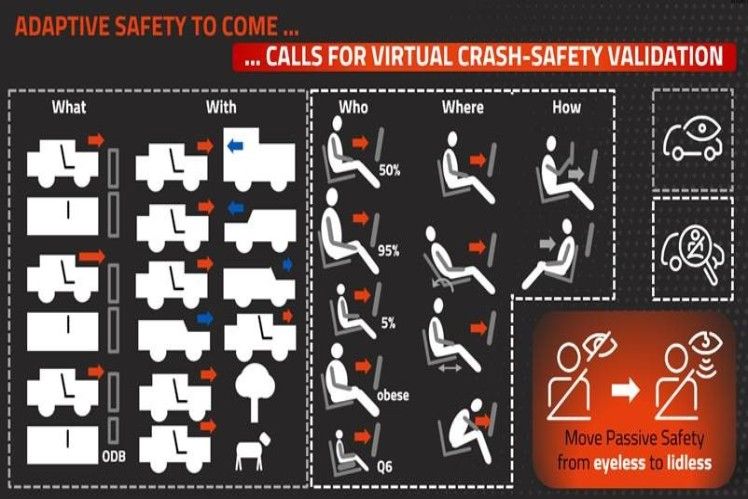
HyDRA®: ultraprecise Test Equipment with a Digital Twin
"When we try, however, to use the traditional methods for developing adaptive restraint systems, we will not meet the target" states Dr. Lars Kübler, Director of Seat Belt Systems Engineering at ZF LIFETEC. "The functional simulation models needed to develop optimal settings for different crash scenarios with various occupants are very difficult to extract from complex full-scale crash tests." Kübler is convinced that: "Adaptive safety requires virtual testing to a much higher level – but this undertaking needs to be based on precise and highly dynamic physical tests."
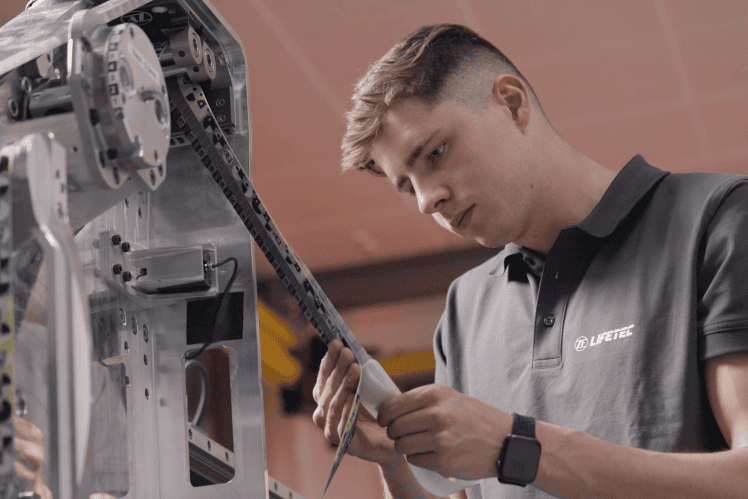
HyDRA® is a test system that perfectly matches this approach. The acronym stands for "Hyper Dynamic Response Actuator." It is an electric driven mini-sled which realizes highly dynamic tests on seatbelt systems with velocities up to 144 km/h and accelerations or decelerations up to 70 g (for reference: At rest, A passenger car accelerates with 0.3 g maximum, a formular one with 1.5 g maximum). HyDRA® is equipped with precise measurement technologies. For instance, inductive displacement sensors can capture every shift at specific measurement points during the crash sequence up to the thousandth of a millimeter. Integrated load cells precisely record the dynamic load in the seatbelt during the crash phases. All these sensors generate data: in essence, a “digital twin” runs in parallel from the very beginning. This is the key advantage of this worldwide unique test system. Therefore, physical tests (expensive and slow) can be replaced by the digital twin with a multitude of virtual tests or simulations (efficient and fast).
Faster Validation Means Faster Development
HyDRA® offers seatbelt system development engineers a wide range of new possibilities such as Lean Validation. "Usually, during seatbelt development, complex system tests are performed for each model of a vehicle manufacturer," explains Machens. "With HyDRA®, we could in the future generate many of these test results with high accuracy by means of virtual tests (simulations). This accelerates the coordination of product application between ZF LIFETEC and customers. In addition, data and simulations based on HyDRA speed up our response time to customer inquiries."
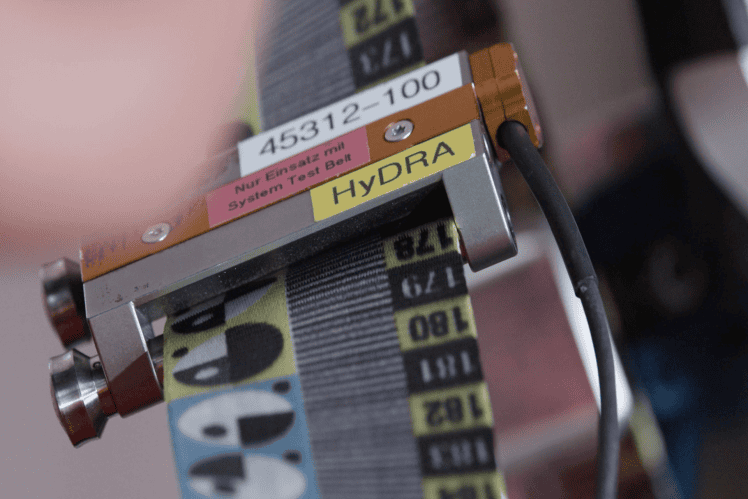
HyDRA® also addresses another trend, which poses additional challenges to traditional sled systems. This is the alignment of crash and pre-crash scenarios, i.e. directly considering maneuvers triggered by driver assistance systems (or by the drivers themselves) generating forces well before the crash. The emergency braking assistant (AEB) is a prime example of a pre-crash system. The AEB system is advantageous in preventing a crash in many cases otherwise it can certainly reduce the impact speed and thus the severity of injuries. Less advantageous is the sharp braking that may cause occupants to shift forward, “consuming” some of the displacement no longer available now for occupant deceleration in the subsequent crash sequence. Machens acknowledges that taking pre-crash activation into account presents a challenge in the development of seatbelt systems today. "With HyDRA®, we succeed." It's no surprise that ZF LIFETEC used HyDRA® to further develop its pre-crash system, including the active belt tensioner ACR8.
Data-Mining: AI and HyDRA® hand in hand
Once the new test system has completed hundreds of tests with standardized and digitized test setups, the data will be used for further analyses such as comparing different design levels during development or across projects. AI algorithms will be employed to identify patterns and characteristics. "In this way we will learn even more from the crash-tests and further accelerate our development work," concludes Machens.
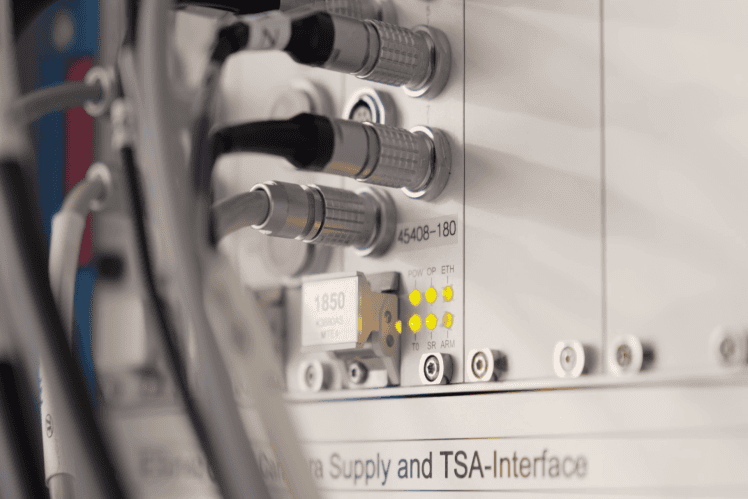
Presentations and Publications
2024 HUMANETICS SAFETY SUMMIT EUROPE, HEIDELBERG, GERMANY HUMANETICS SAFETY SUMMIT EUROPE
2024 HUMANETICS SAFETY SUMMIT EUROPE, HEIDELBERG, GERMANY
CONNECTING HUMANS IN MOTION
RESTRAINT ANALYSIS ON HyDRA® TO FOSTER REAL-LIFE SAFETY
- Dr.-Ing. Kai-Ulrich Machens, Manager Seat Belt Systems Engineering, ZF LIFETEC
- Dr.-Ing. Lars Kübler, Director Seat Belt Systems Engineering, ZF LIFETEC
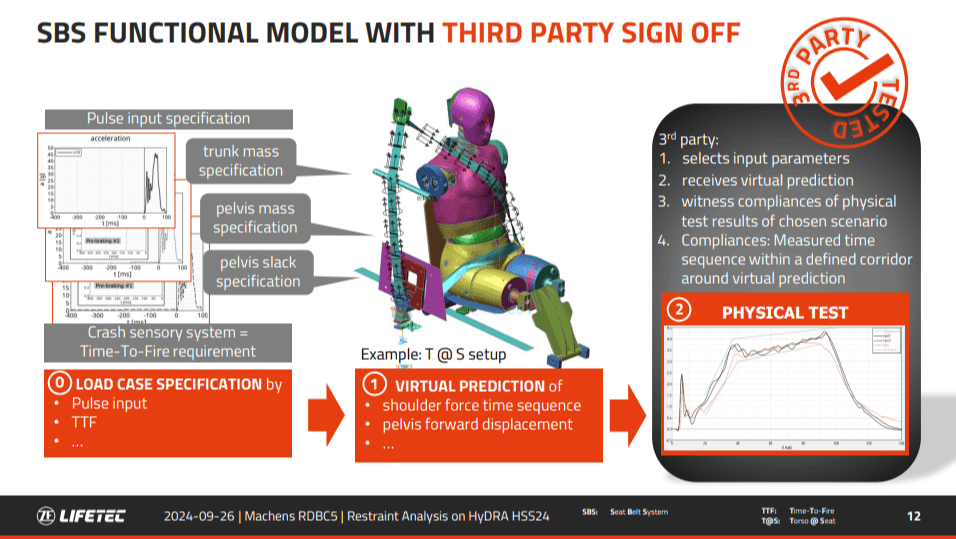
2024 crash.tech 2024, Ingolstadt, Germany Crash.tech 2024
International conference TÜV SÜD, Technische Hochschule Ingolstadt, Esplanade 10, Ingolstadt, 13 März 2024
HyDRA®: DESIGN SPACE VALIDATION FOR SEATBELT SYSTEMS COMBINED WITH FUNCTIONAL MODELS FOR REAL-LIFE SAFETY
- Dr.-Ing. Kai-Ulrich Machens, Manager Seat Belt Systems Engineering, ZF LIFETEC
- Dr.-Ing. Lars Kübler, Director Seat Belt Systems Engineering, ZF LIFETEC
2023 27th ESV 2023, Yokohama, Japan 27th ESV 2023
27th International Technical Conference on the Enhanced Safety of Vehicles (ESV) Convention Center “PACIFICO“ Yokohama North, Japan, 5 April 2023
DYNAMIC TESTING WITH PRE-CRASH ACTIVATION TO DESIGN ADAPTIVE SAFETY SYSTEMS
- Dr.-Ing. Kai-Ulrich Machens, Manager Seat Belt Systems Engineering, ZF LIFETEC
- Dr.-Ing. Lars Kübler, Director Seat Belt Systems Engineering, ZF LIFETEC
2022: Airbag 22, Mannheim, Germany Airbag 2022
15th International Symposium and Exhibition on Sophisticated Car Safety Systems Convention Center “Rosengarten“ Mannheim, Germany, 29 November 2022
HyDRA®: PHYSICAL & VIRTUAL DYNAMIC TEST-BENCH TO APPROACH INTEGRATED SAFETY
- Dr.-Ing. Kai-Ulrich Machens, Manager Seat Belt Systems Engineering, ZF LIFETEC
- Dr.-Ing. Lars Kübler, Director Seat Belt Systems Engineering, ZF LIFETEC
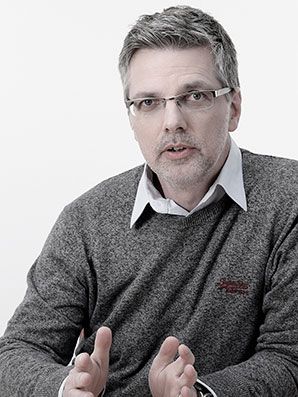
Andreas Neemann wrote his first ZF text in 2001 about 6HP transmissions. Since then, the automotive writer has filled many publications for internal and external readers, showcasing his passion for the Group's more complex subjects.
Next Stories
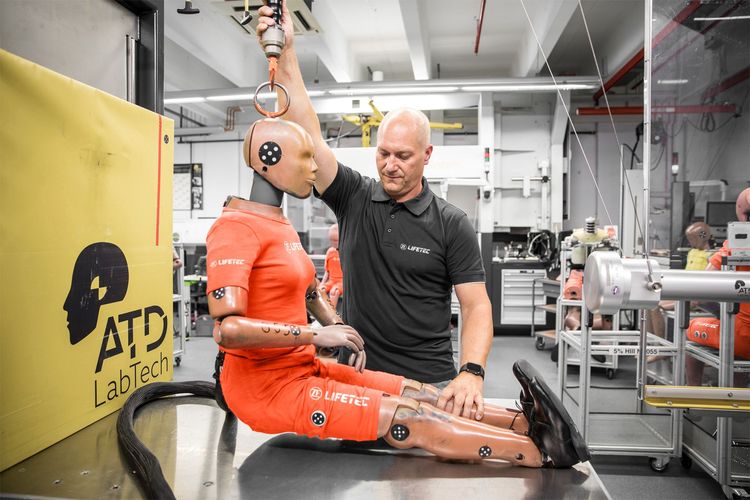
Behind the Scenes: Look into the Dummy Laboratory
When it comes to global occupant safety systems such as airbags and seatbelts, ZF is the leader, as is widely known
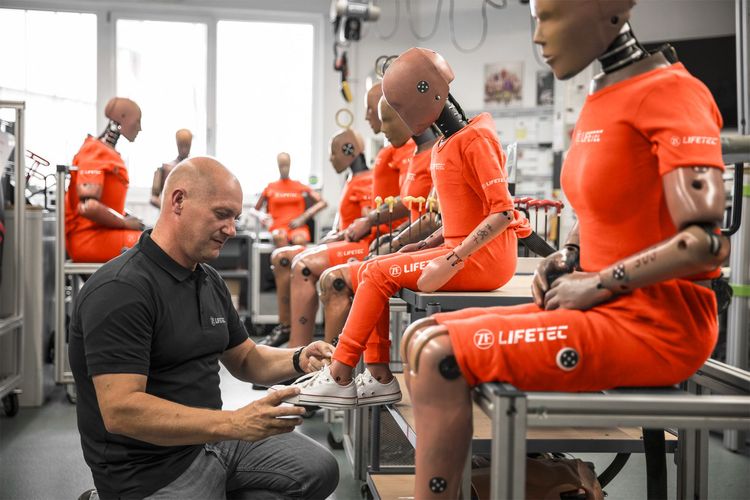
The “Crash Clan” Protects Us
How dare we call them “dummies”! They are actually a family of intelligent specialists who make an enormous contribution to occupant safety. It’s time to get to know them better.