Convincing test experience
When it comes to global occupant safety systems such as airbags and seatbelts, ZF is the leader, as is widely known. What is not quite so commonly known is that crash tests actually take place here all the time – 24 hours a day, 7 days a week. ZF is among approximately 100 companies worldwide that regularly perform component-level tests with crash test dummies (anthropomorphic test devices, or ATD).
This expertise is based in the Passive Safety Systems division in Alfdorf, Germany. The location has dealt with safety issues since the 1970s. Back then, executive managers and other volunteers sometimes even served as live crash test dummies. Although this was admittedly an impressive way of convincing customers of the effectiveness and quality of safety solutions, it is no longer practiced today for good reasons.
In any case, the former Repa GmbH (a fine-blanking and refurbishment plant), the German specialist for seatbelts and later also airbags, set up a new, second plant in Alfdorf at that time. The capital for this was provided through a 70 percent stake held by the US Group TRW. And this was acquired by ZF in 2015.
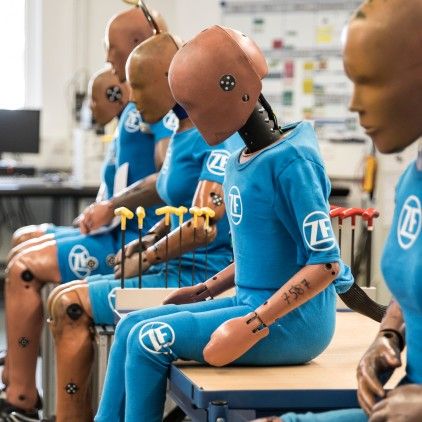
Enhanced safety thanks to 7,000 dummy crashes
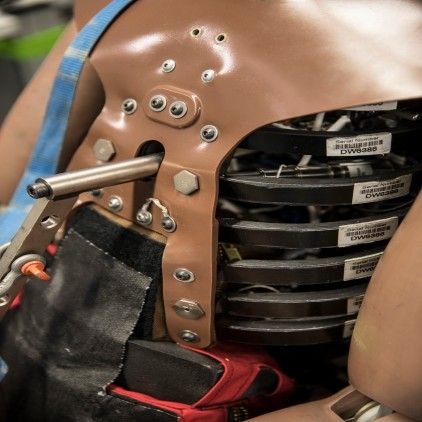
Preparing, checking, and repairing ATDs
Seated safety
Like myself, most laboratory experts are trained electrical engineering technicians, because the job requires them to handle sensors and data with confidence. Whatever qualifications are required beyond that are based on interest and experience. Of course, there is training, such as the one that had to be done recently for the latest, particularly human-like (biofidelic) and complex THOR dummies. The test requirements themselves are also currently changing. The trend toward fully automated driving and electric cars with a level floor raises hopes for many new seating positions and settings. But each and every one of them must be tested in terms of occupant stress and safety before they can be implemented in a series-production vehicle. This diversity can only be covered by virtual crash simulations on a computer. Nevertheless, the ATDs in the ZF laboratories need not fear the future: the data on which these simulations are based can be obtained only through crash tests involving actual dummies.
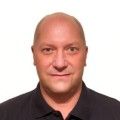
Sven Turza is team leader of the ZF dummy laboratory in Alfdorf.
Next Stories
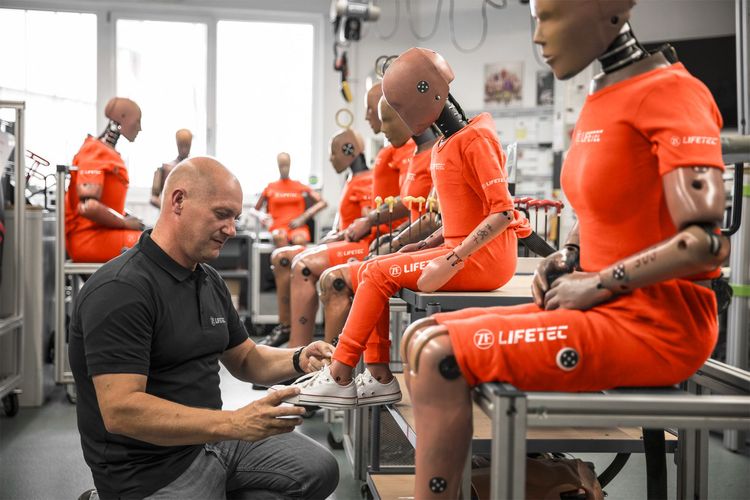
The “Crash Clan” Protects Us
How dare we call them “dummies”! They are actually a family of intelligent specialists who make an enormous contribution to occupant safety. It’s time to get to know them better.
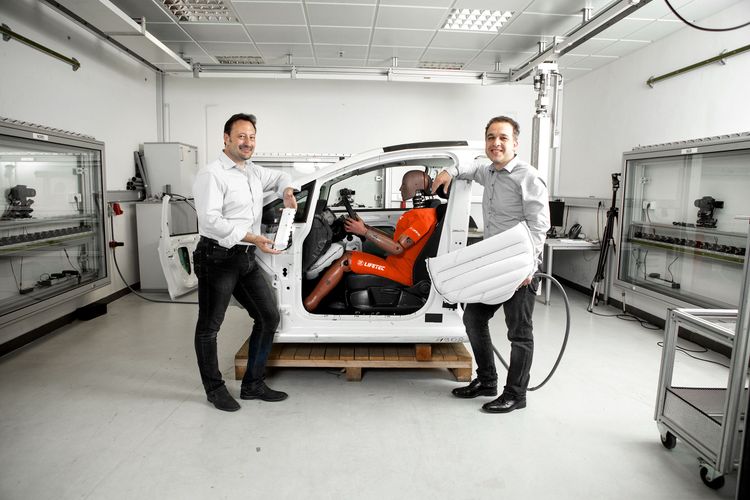
Meeting the Challenge of Knee Airbags
One of the most exciting parts of the automotive industry is the idea that there is always a way to make something lighter, smaller, safer.