Every year in Germany, the third Saturday in June is declared "Road Safety Day", which is intended to inform and remind you of the topic of safety in our daily driving. In terms of traffic safety we can no longer imagine vehicles without it and ZF is proud to be a part of this success story. It has been a long journey with many twists and turns. This year marks the 70th anniversary of the first airbag patent application.
After initial tests with pneumatic restraint systems in the aviation industry had already been carried out in the 1920s, on October 6, 1951, the Munich engineer Walter Linderer filed a patent (DE 896312) for the protection of persons in vehicles against collision injuries. The visionary described his idea at the time with the explanation: "According to the invention, an inflatable container is assembled in a folded state in front of the seat of the person to be protected, which in case of danger automatically or by arbitrary activation inflates so that the person in question is not subjected to injury or the injury is mitigated in the event of a collision."
Two years later, in November 1953, Linderer was granted the patent. In the same year, John W. Hetrick was granted a patent (US 2 649 311 A) for an airbag concept in the USA.
Both systems had the same objective, but implementation - namely to generate extremely short inflating times in a closed vehicle using highly compressed air - was an insurmountable obstacle. They were unfortunately unsuccessful. A few other inventors tried the idea, but failed due to insufficient functional reliability. In the end pyrotechnics were required to achieve the extremely short inflating time required for the airbag.
At the beginning of the 1970s, a few thousand vehicles were produced and equipped with airbags on the American market, but there was considerable resistance to the new, expensive systems and the technology was not yet perfectly mature. The actual development of the current pyrotechnic gas generators, which allow for a response time of less than 30 milliseconds, was developed 20 years later in southern Germany. Meanwhile, the export of German passenger cars to the USA had become an important economic factor. The German automotive industry also endeavored to find a solution because of the prescribed law, which made inflatable occupant safety systems mandatory for new cars in the USA as of January 1, 1973. From a military project at ZF (formerly Bavaria Chemie/Temic/TRW), the task was to "transmit small scatter bombs from the aircraft by means of a propellant charge in such a way that the sound pressure generated during the emission does not cause any damage to the aircraft," and a gas generator was the principle way to achieve this. The solid fuel initially consisted of sodium azide, potassium nitrate and sand and was pressed in tablet form. It exclusively produces the non-toxic gas nitrogen and potassium oxide as solids when ignited.
At that time, Daimler-Benz was strongly committed to new standards for safety technology. In just a few days, the first gas generator for the airbag was designed at the Bavarian chemistry company location that is now part of ZF in the winter of 1970/71. About ten years later it was to be used in the Mercedes-Benz S-Class under the leadership of Daimler-Benz and in cooperation with Petri, who supplied the airbag and the cover on the steering wheel in 1981. Shortly afterwards, BMW and other manufacturers joined in.
But what does it require to create a cushion which is located at the front of the steering wheel and is inflated within a few milliseconds in the event of a crash and into which the driver’s head and chest contacts? If you imagine putting pyrotechnics in front of the driver's nose in a car, which then triggers and ignites, you can imagine that testing this technical development takes time and careful examination of the process.
First, the entire sensor system must be developed for the vehicle in order to detect a crash quickly and accurately so that the triggering of the airbag can be timely deployed. For example, it must not be just a small object or a crash at very low speeds that triggers a deployment, a significant crash must really have taken place. In the event of an accident, the crash sensors detect the impact, sends the data to the airbag control unit and a signal is sent to the gas generator to ignite. A thin wire is heated by an ignition current which activates the inflator tablets. The crash or acceleration sensors are typically located in the front and rear bumpers or door panels for side impacts. The very first sensors were not electronic sensors (like today's electronic deceleration sensors), but mechanical: You can imagine it as a small roll that has been rolled up, with a button in the middle and when the deceleration has an effect on it, it rolls out and triggers.
But how does the sensor system distinguish between the vibrations - whether it is actually an impact or a curb?
To do this, the pulses must be measured - each pulse has a certain strength and a vectorial direction. This impulse is based on mathematical algorithms which quickly calculate whether this impulse rate requires an airbag deployment. Connected to the vectorial direction (if the impact comes from the front, from behind or the side), the sensor evaluates the strength, the course and the direction of the pulse and whether the airbag is triggered or not. Airbag technology and especially the sensors, has been further developed. The sensors are better shielded from external influences, false triggering has been nearly eliminated, and contacting also improved. From the turn of the millennium onwards, two-stage gas generators were also developed, enabling the airbag deployment to be more customized to the crash and occupant characteristics such as speed of the collision, and the size and relative position of the occupants in relation to the airbag thus transferring less energy to the occupants in certain crash scenarios. In order to help avoid incorrect system triggering, at least two airbag sensors are always installed.
Regarding gas generators to fill the airbag, a distinction can be made between three different technologies:
1. Purely pyrotechnic generators: These contain pyrotechnic tablets which are ignited and which generate pure gas and heat when burned, which then reacts, expands and fills the airbag. For this purpose, a pyrotechnic formulation in pressed tablet form is produced at ZF and installed in the gas generator area. This is often referred to as an explosion - but technically it is a burn-off because it subsides after a certain pressure function phase, whereas an explosion is immediate and short-lived. Nevertheless, an extremely loud bang remains and there are pyrotechnics in the vehicle.
2. The pure compressed gas generator: it is usually filled with helium or an argon-helium mixture. When the generator is opened by an impulse, it flows into the airbag. Initially, tests were carried out with a pure compressed gas generator, i.e. without pyrotechnic charge to generate the gas. This did not work because the gas did not flow out quickly enough or was in some cases freezing due to the rapid outflow. Helium is very sensitive to leakage: isolating a helium gas generator with approx. 250 bar for ten to fifteen seconds without gas leaking is very difficult.
3. In order to reduce the gas temperature, hybrid gas generators were also developed - the hybrid version is a combination of the other two versions: Here, a small pyrotechnic charge in tablet form is used to initiate the deployment, while the main gas quantity comes from a compressed gas generator, opened by means of pyrotechnics and then supplies a specified volume of air.
In current systems, the pyrotechnic version is usually used for front airbags and the hybrid or pure gas version is used for side applications. Towards the end of the 1990s, the Sodium Azide fuel was phased out with new chemical formulations more free of acidity, which are still used in numerous generator variants today.
The gas generators developed by ZF have become increasingly variable and effective over time - although they have become smaller and lighter in order to be integrated into countless, flexible safety packages.
ZF Passive Safety Systems business offers full occupant safety system solutions for integrated vehicle safety, and it is important to note that airbag systems are one part of a highly coordinated systems approach that includes advanced seat belt restraints that work in combination with airbags to help protect passengers and mitigate the potential effects of an accident.
As we celebrate Road Safety Day we can be proud of the contributions that ZF and the industry have made in making today’s vehicles safer than ever before and look forward to more safety innovations in the future.
Next Stories
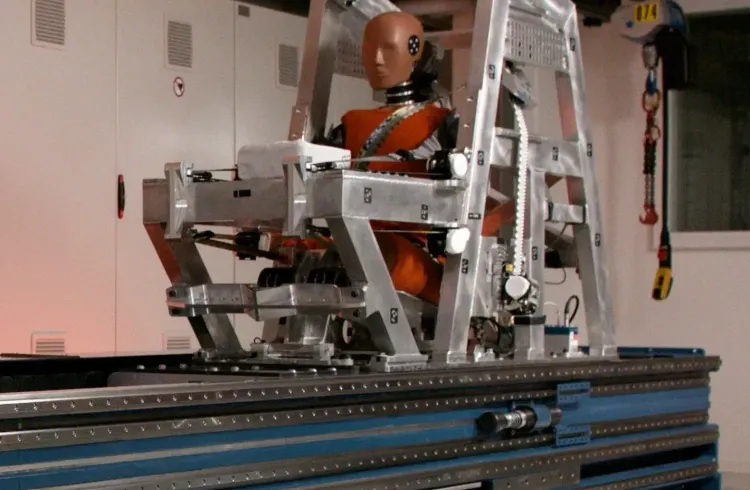
HyDRA®: Full electric crash-sled shortens development time
Precise sensors and digital interfaces allow HyDRA® to accelerate the development of seatbelt systems with highly dynamic testing.
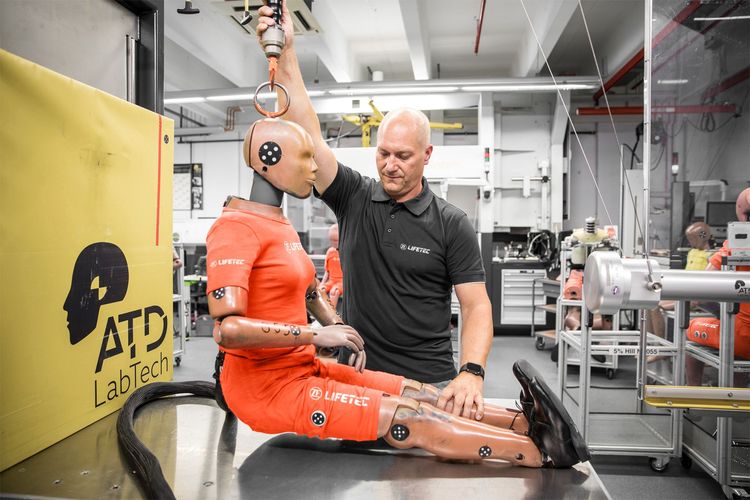
Behind the Scenes: Look into the Dummy Laboratory
When it comes to global occupant safety systems such as airbags and seatbelts, ZF is the leader, as is widely known