Es gibt immer einen Weg, etwas leichter, kleiner oder sicherer zu machen. Dieser Ansatz ist einer der spannendsten in der Automobilindustrie und fördert ein Umfeld ständiger Veränderungen und das Streben nach immer neuen Innovationen. Manchmal ist es wie ein Abenteuer in unbekannten Gebieten – eine Idee treibt die Entwickler voran und verlangt nach Innovationen jenseits der bekannten Technologien.
Vor einigen Jahren erkannten wir einen klaren Trend: Unsere OEMs suchten nach Möglichkeiten, Gewicht und dadurch den Kraftstoffverbrauch zu reduzieren. Gleichzeitig wollten sie kleinere Module, die sich gut in die neuen Innenraumdesigns integrieren ließen. Deshalb beschlossen wir, einen Knie-Airbag zu entwickeln, der alle diese Anforderungen erfüllt. Die Ziele waren sehr ehrgeizig: 30 Prozent Gewichtsreduzierung bei einem Airbag, der kleiner als alle bis dahin bestehende Modelle sein sollte – ohne Kompromisse bei Stabilität und Funktion!
Wie bei jedem Abenteuer haben wir mit einer umfangreichen Recherche begonnen. Das Entwicklerteam zog zahlreiche Möglichkeiten in Betracht und untersuchte das Gewicht der einzelnen Komponenten, um die Anforderungen zu erfüllen. Schließlich kamen wir zu dem Schluss, dass das Airbag-Gehäuse das größte Potenzial zur Gewichtseinsparung aufzeigte.
Dies war der Beginn einer langen, herausfordernden Reise: Das Metallgehäuse durch Kunststoff zu ersetzen, würde nicht genügen, um den Anforderungen zu genügen. Wir haben mehrere Ansätze in Betracht gezogen. Einige davon landeten in der Kategorie "Kann nicht funktionieren" und andere in der Kategorie "Gibts nicht". Es kristallisierte sich heraus, dass die Idee mit dem größten Potenzial eigentlich unmöglich war – das Metallgehäuse durch Gewebe zu ersetzen!
Dies erforderte eine völlig neue Generation an Knie-Airbag-Modellen sowie spezielle Prozesse und Herstellungsmethoden, die sich von der traditionellen Technologie zur Herstellung von Stahlgehäusen unterschieden.
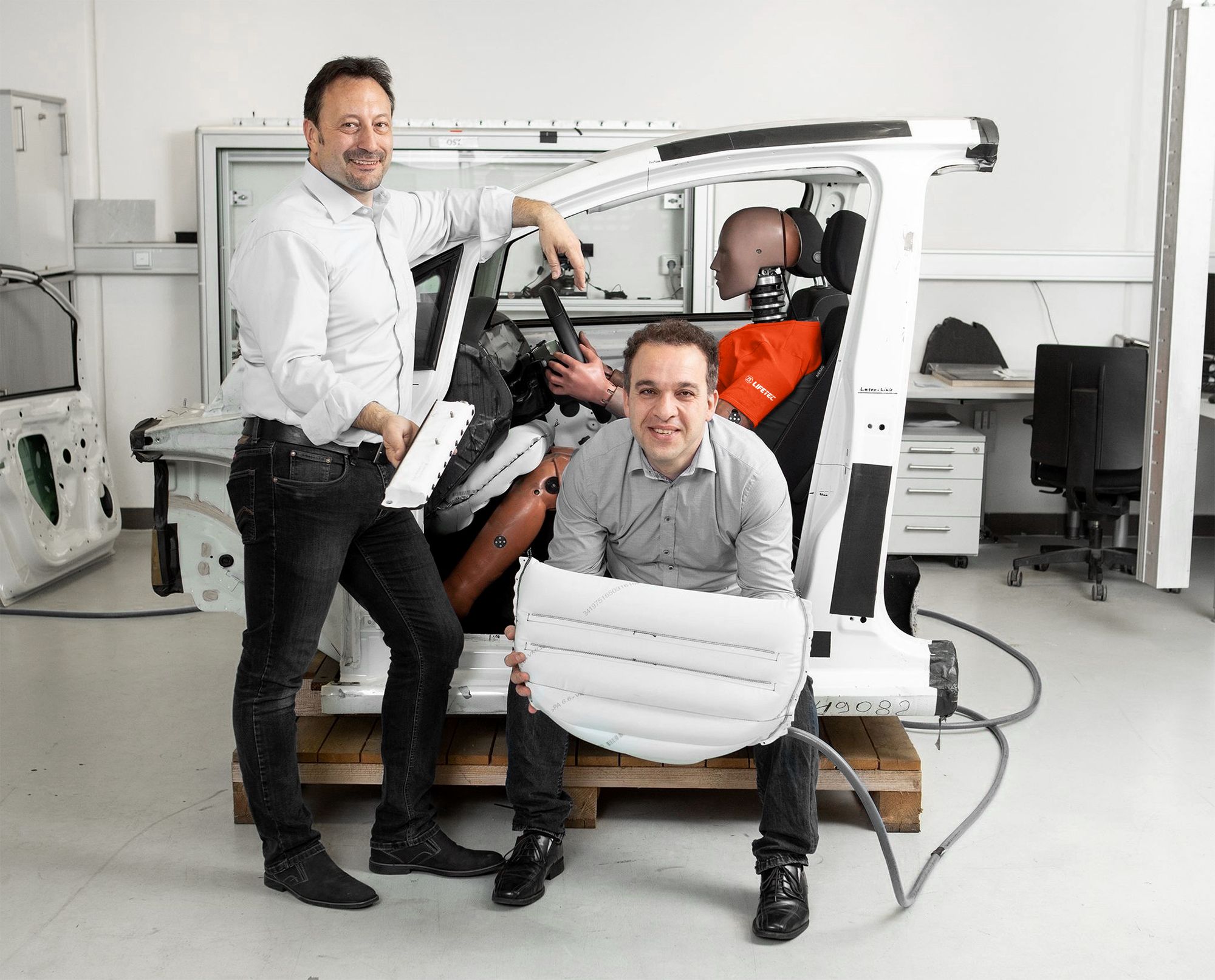
Warum ist eine solche Innovation wichtig?
Eine solche Innovation bringt den Fahrzeughersteller erhebliche Einsparungen bei den Rüstkosten, eine schnellere Verfügbarkeit von Prototyp- und Serienteilen während der Entwicklung und eine größere Flexibilität bei erforderlichen Änderungen des Gehäusedesigns. Der Knie-Airbag wird außerhalb des Sichtfeldes eingebaut, so dass nur eine Schutzabdeckung benötigt wird und somit keine Veränderungen im Armaturenbrett vorgenommen werden müssen. Das erhöht die Freiheit der Innenraumgestaltung.
Für den Endverbraucher bedeutet die Reduzierung der Gehäusegröße um 20 Prozent (Höhe des Gehäuses 50 Millimeter bei einem Metallgehäuse gegenüber 40 Millimeter bei einem Gewebegehäuse) mehr Beinfreiheit und Komfort für die Insassen.
Wir haben ein Produkt entwickelt, das nicht nur den identifizierten Herausforderungen gerecht wird, sondern auch in die Zukunft konventioneller und autonom fahrender Fahrzeuge investiert. Unser Team ist stolz auf die erfolgreiche Entwicklung und Markteinführung des Knie-Airbags mit Gewebegehäuse.
Wir haben nicht nur von unseren Kunden positives Feedback bekommen, sondern auch innerhalb und außerhalb des Unternehmens Anerkennung durch den Gewinn von zwei renommierten Preisen erhalten: den ZF Excellence Award in der Kategorie Produkte und den Altair Enlighten Award in der Kategorie, die jedes Jahr die beste Innovation im Leichtbau auszeichnet.
Für mich ist das Spannendste, dass dieser Erfolg die Grundlage für unser nächstes großes Abenteuer ist.

Werner Freisler ist Produktverantwortlicher Core Manager für Knie-Airbags bei ZF in Alfdorf
Nächste Stories
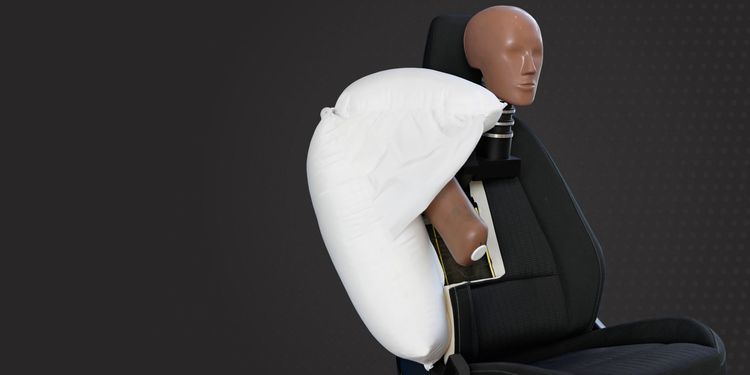
Ein Airbag, der blitzschnell zur Seite steht
Ein Seitencrash kann bei Pkws äußerst gefährlich sein. Das gilt sogar für die gegenüberliegende Seite des Insassen – denn der Impuls kann seinen Oberkörper in Richtung Fahrzeugmitte schleudern.
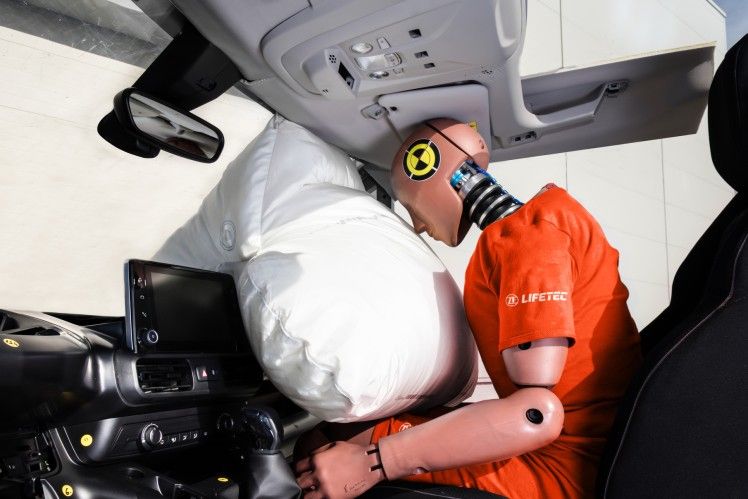
Neuer Airbag aus dem Himmel
ZF gilt als Pionier des Beifahrer-Dachairbags. Er hilft, Personen unterschiedlichster Größe und in verschiedenen Sitzpositionen zu schützen. Der im Dachhimmel verbaute Airbag kann eine sinnvolle Alternative zu herkömmlichen Airbags darstellen.