ZF LIFETEC verbessert Insassenschutz durch innovative Testmethoden
2024-Sep-11- Umfassende Testverfahren sichern Innovation und Qualität zu kompetitiven Preisen
- ZF LIFETEC entwickelt weiter an einem physikalischen und virtuellen (hybriden) Testkosmos und beschleunigt so Entwicklungszyklen
- Fokus auf Wettbewerbsvorteil für Kunden kombiniert mit klarer Mission und „Real Life Safety“-Anspruch
- ZF LIFETEC fokussiert Testing und Entwicklung in drei zentralen Tech-Centern und weiteren Standorten in Europa, Amerika und Asia Pacific
Wenn Beschleunigungen jenseits der 50g an Dummies zerren, Testschlitten in einem Augenblick von null auf hundert beschleunigt werden, um Daten zu erzeugen und um mit physikalischen und virtuellen Tests neue Designs und Produkte zu validieren und Lenkräder, Gurte und auch Airbags in Dauertestapparaturen gequält werden klingt das nicht unbedingt sicher - sorgt aber für mehr Sicherheit. Zumindest wenn das Geschehen in einem der mehr als 20 Testzentren oder in den drei zentralen Tech-Centern von ZF LIFETEC in Europa, Nordamerika und Asien angesiedelt ist.
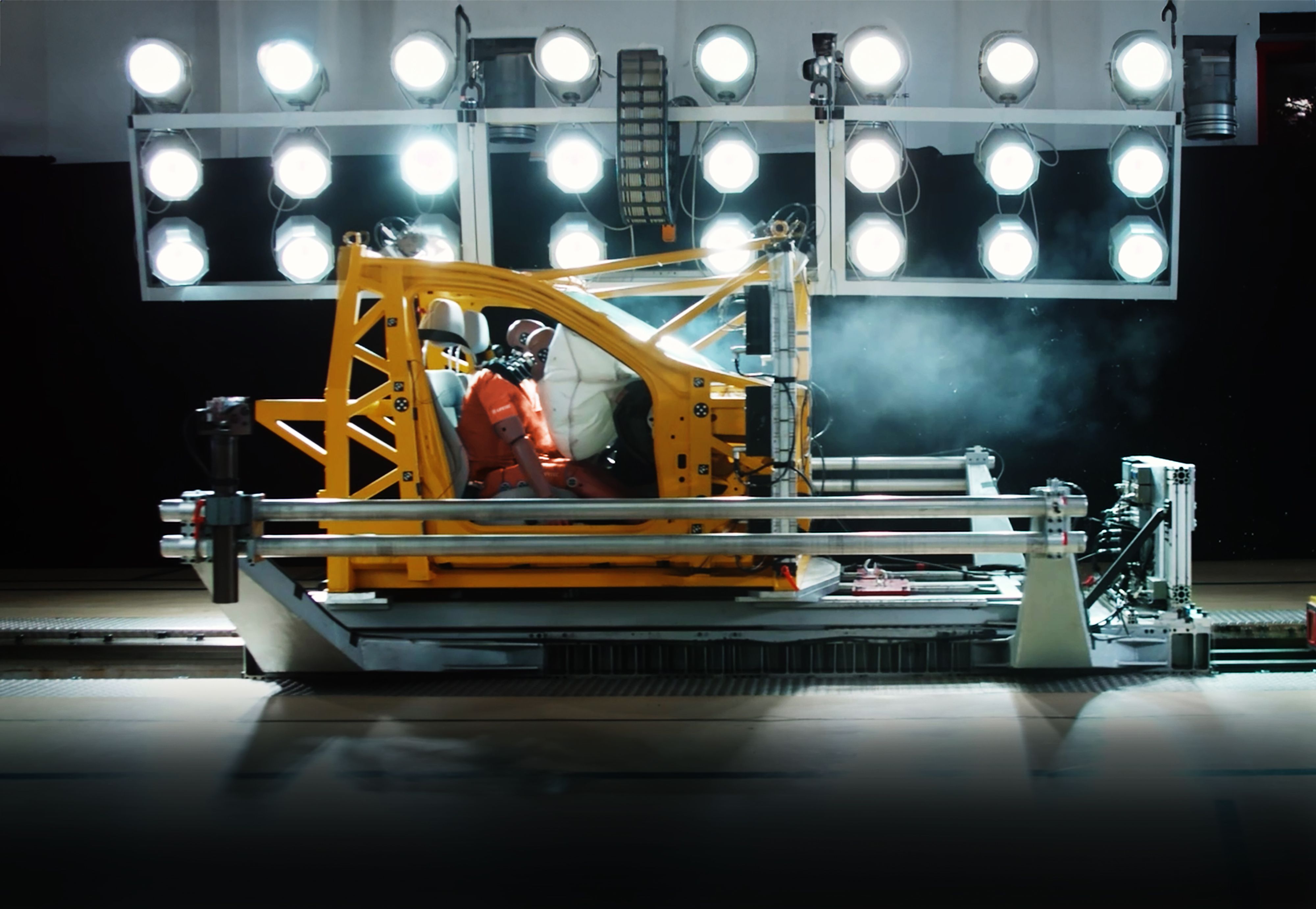
Gurte, Airbags und Lenkräder werden unter härtesten Prüfbedingungen getestet, um höchste Qualitätsstandards zu garantieren. ZF LIFETEC konzentriert sich dabei nicht nur auf Testkompetenzen, die über Jahrzehnte hinweg aufgebaut wurden, sondern stößt zusätzlich auch in neue, virtuelle Testbereiche vor. Damit verkürzt ZF LIFETEC die Entwicklungszyklen von Fahrzeugen, um seinen Kunden somit einen klaren Wettbewerbsvorteil in internationalen Märkten zu geben. Die Vision ist dabei klar definiert: Die Insassensicherheit immer mehr an reale Unfallszenarien (Real Life Safety) anzupassen und so die Unfallfolgen im Straßenverkehr für Betroffene noch weiter zu verringern.
Was mit der Einführung von Sicherheitsgurten in den 1970er-Jahren begann und mit der Einführung von Airbags in den 1980er-Jahren fortgesetzt wurde, ist heute quasi Standard in der automobilen Sicherheitstechnik. Um diese lebensrettenden Fahrzeugsysteme stetig zu verbessern haben sich die Standards für deren Test immer weiterentwickelt. Crashversuche der Automobilhersteller sind spätestens seit den 1970-Jahren üblich und auch bei ZF LIFETEC als einem der führenden Systemanbieter für passive Sicherheitstechnik für Fahrzeuge werden weltweit mehr als 50 dynamische Tests pro Tag durchgeführt. Neu hinzugekommen sind jüngst digitale Test- und Validierungsverfahren, die durch physikalische Versuche bestätigt werden.
Dadurch werden Sicherheitskonzepte noch besser an den individuellen Insassen angepasst. Denn im Fokus des Real-Life-Safety-Ansatz steht der Mensch als Individuum und das Ziel, diesen noch besser zu schützen – angepasst an die individuelle Statur, Geschlecht und Alter. Für diesen adaptiven Ansatz des Insassenschutzes stehen eine Vielzahl von Lösungen und Strategien zur Verfügung, die nur durch eine Kombination aus physikalischem Test und virtueller Validierung entwickelt und getestet werden können.
Die ganzheitliche Bewertung einer Testreihe basiert auf einer großen Anzahl von Einzellastfällen, die zum Beispiel die Komponenten eines Sicherheitsgurt-System unterschiedlich belasten. Denn um auch kritische dynamische Belastungen rechtzeitig erkennen und richtig entgegenwirken zu können, müssen alle wesentlichen dynamischen Belastungen des Gurtsystems (Kraftniveaus, Auszugsweg und Geschwindigkeit) einschließlich Pre-Crash Dynamik erfasst werden. Das gilt ebenso für den gesamten Insassenschutz. Dieses Gesamtbild ohne das Zusammenspiel aus realen und virtuellen Tests zu entwickeln, würde einen sehr hohen Zeit- und Ressourcenaufwand bedeuten. „Das ist ein attraktives Zukunftsthema, denn die Adaptivität von Rückhaltesystemen wird von den NCAPs als Entwicklungsziel in ihrer aktuellen Roadmap vorgegeben und in Crashtest-Bewertungen entsprechend honoriert“, so Harald Lutz, Entwicklungsleiter bei ZF LIFETEC.
Weltweite dynamische Versuche
Ein weiterer wesentlicher Faktor für Innovation und Qualität sind Testing-Expertise und Equipment. Das gilt für die Tests von Einzelkomponenten, aber auch für Tests kompletter Systeme. Als dynamischer Test wird dabei das Zusammenspiel – beispielsweise von Gurt und Airbag – im Einzelnen oder als Gesamtsystem in Crashsimulationen auf technisch komplexen Schlittenanlagen bezeichnet. ZF LIFETEC verfügt über Schlittenanlagen in fünf zentralen Märkten (USA, Japan, Italien, China und Deutschland). Alle Versuche werden von Testingenieuren und -technikern weltweit zuverlässig umgesetzt, gemäß den Anforderungen, die Sicherheitsbewertungsorganisationen wie Euro NCAP, China NCAP, US NCAP oder auch durch die US-Vorschriften des Federal Motor Vehicle Safety Standard (FMVSS) an die internationalen Automobilhersteller stellen.
ZF LIFETEC entwickelt und digitalisiert das Testing konsequent weiter. Das Unternehmen nutzt dabei die Erfahrung und nicht zuletzt die immensen Datenmengen der bisherigen Tests, um das Prüfgeschehen immer stärker zu virtualisieren. „Simulationen werden die Realtests nicht ersetzen, aber ein guter Mix aus Simulation und Realtest macht das Testing in Zukunft deutlich effizienter“, erklärt Lutz. Eine wichtige Grundvoraussetzung für virtuelles Testing ist die Validierung der, dabei zu Grunde gelegten, Annahmen. Nur so kann sichergestellt werden, dass virtuelle Tests mit der Realität übereinstimmen. Um das zu gewährleisten, hat ZF LIFETEC die sogenannte HyDRA (Hyper Dynamic Response Actuator) entwickelt. Dieser, in der Branche einzigartige, Prüfstand ermöglicht einen schnellen und präzisen Abgleich zur Realität. Damit wird ein digitaler Zwilling validiert, der deutlich verkürzte Entwicklungszyklen ermöglicht und als Enabler für „Real-Life-Safety“ dient.
Spezialist bis auf Komponentenebene
Wer in der Entwicklung und Produktion von Rückhaltesystemen Technologieführer ist, muss auch beim Testing von Komponenten eine sehr hohe Bandbreite abdecken: Denn es geht um die Entwicklung von Textilien für Gurte und Airbags, von Metall- oder Kunststoffgehäusen bis hin zu pyrotechnischen Treibladungen und hochpräzisen Sicherheitssystemen. Vor allem in der Prototypenphase stehen für alle Komponenten umfassende Material- sowie Umwelt-Simulationstests auf der Agenda. Dabei werden – oft mit Hilfe speziell entwickelter Prüfstände – Alterungs- und Abnutzungsprozesse unter realistischen Bedingungen zeitlich gerafft und durchgespielt. Konkret wird auf diese Weise beispielsweise der Einfluss von Salzwasser-, Sonnenlicht- oder Staubeinwirkung bis hin zu thermischen Veränderungen oder Vibration ermittelt, um Beeinträchtigungen für die spätere Funktionsfähigkeit auszuschließen.
Zudem gilt es, sämtliche Systeme auf elektromagnetische Verträglichkeit zu prüfen. Bei Lenkrädern, die als Mensch-Maschinen-Schnittstelle (HMI) eine zentrale Rolle für die Sicherheit und die Kontrolle eines Fahrzeugs einnehmen, ist das beispielsweise wichtig, um Funktionen wie das Hands-on-Detection ausfallsicher auszulegen.
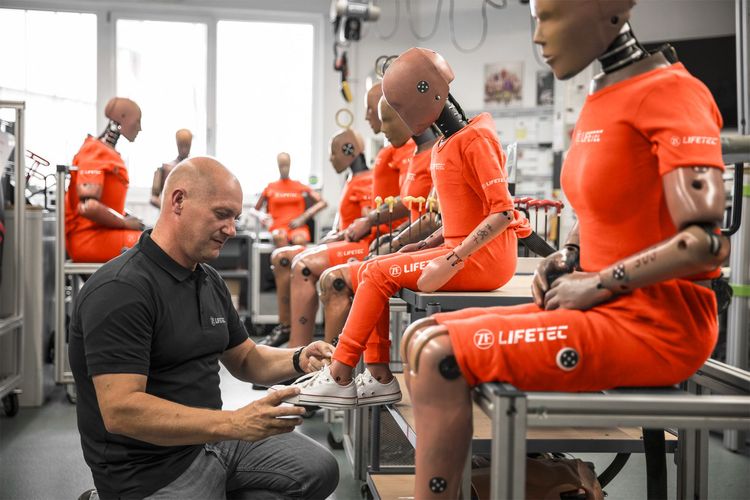
Ravi Kumar Tirumukulu, Executive Director, ZF LIFETEC India; Akash Passey, President, ZF Group Region India; Hon'ble Minister Sri. Duddilla Sridhar Babu Garu, Minister for IT & Industries, Govt. of Telangana and Rudolf Stark, Executive Vice President, ZF LIFETEC (f.l.t.r.) during the opening ceremony of the new Global Capability Center in Hyderabad, India.